一、首先將礦粉與煤、水按一定比例配制后送往制球機,制成球輸送到窯尾,通過氧化鋅回轉(zhuǎn)窯的不斷轉(zhuǎn)動進入窯尾的配料不停地進入烘干和預(yù)熱段(12m左右,650-700度)然后進入中溫段(18m左右,700-850度)最后進入高溫段(18m左右,850-1100度,907度是Zn的沸點)。窯子不停轉(zhuǎn)動,在高溫段翻動料面上產(chǎn)生很大很濃的黃色火焰,即鋅蒸汽和各種金屬蒸汽,隨著窯內(nèi)的強大的引風和鼓風 )逆向進入中溫段、預(yù)熱段、烘干段,同時與窯內(nèi)的剩余氧氣進行反應(yīng)產(chǎn)生ZnO粉塵,但由于風量和風速(3-4m/s)較快,一下到達氧化沉降室.
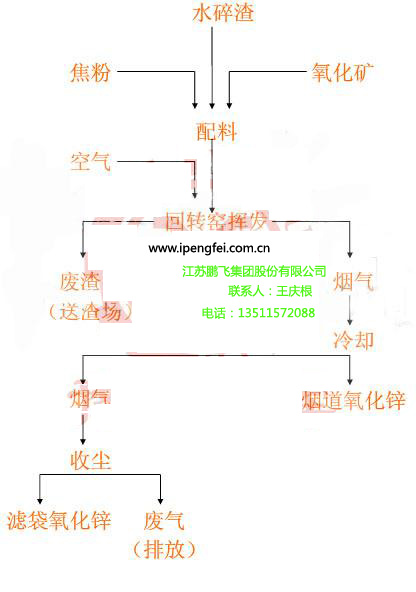
二、氧化沉降室的工作原理(余熱鍋爐)將回轉(zhuǎn)窯送進來的流速為3-4m/s 的高溫并含有各種部份氧化物及粉塵的氣體進行分離,散熱和繼續(xù)氧化。(1)分離作用將比重比較大點物質(zhì)(主要是指各種氧化不了的雜質(zhì)沉降除掉,屬第一次分離)(2)將高溫段的氣體通過水冷壁管吸收部分熱量,收集產(chǎn)生蒸汽利用,降溫在250-300度左右。(3)將沒有完全氧化物質(zhì)繼續(xù)在此段氧化,完全產(chǎn)生各種氧化物質(zhì)(粉塵比重比較輕點),此粉塵和部分比較輕的粉末,經(jīng)過風量的氣流,進入冷表系統(tǒng),總之沉降室的溫度高底可以通過配比,壓縮用汽量和調(diào)整引風機的風量等方法來解決。
三.冷表系統(tǒng)的工作原理
1、將高溫氣體(300-400度)通過11組人字管散熱降溫達到出口時,氣溫不能超過160度,如果達不到將人字管槽水位加深,增加熱量的吸收,如遇冬季寒冷氣候,各個設(shè)備散熱都比較大,到時看輸入收塵器的氣溫達不到130度時,則將人字管槽內(nèi)水降低或少走人字管通道,后有三組可作調(diào)整氣溫。
2、將進入的高溫氣體帶來的氧化物和部分粉塵,此粉塵的比重比氧化物的比重要大些,所以通過11組人字管逐步按比重的大小分級沉降在11個斗內(nèi),起到了第二次分離作用,當然也有部分氧化物與粉塵一起沉降在前幾個斗內(nèi),這是難以分離的,主要因為它們比重接近和氣體的濃度比較大、流速比較快3-4m/s等原因(相互碰撞結(jié)合成較大的顆粒)
四、吸塵器的工作原理
1、將進入來的160度左右并帶著很濃氧化物及粉塵氣體通過脈沖方式進行氣、粉分離。通過直徑130mm的耐高溫(160度以下2212個)袋子分離成粉塵及二氧化硫氣體,粉塵進入灰斗,二氧化硫氣體通過引風機送入脫硫塔。
2、通過分離的過程,同時將氣體溫度降至60度
五、脫硫塔的工作原理
1、將進入的二氣化硫氣體及其他氣體,從脫硫塔底部進入向上流動,而堿液從上往下進行三級霧狀流下,并通過三級空心球進入方向的改變及減速向上移動,
從而達到酸堿中和的目的,最后排放的氣體含硫量不超過400毫克。
2、通過酸堿中和會產(chǎn)生亞硫酸鈣(沉淀物)及時抽出,通過壓濾機將水和渣分離回籠使用,亞硫酸鈣作為為廢渣排出。